Vincent Pluvinage, CEO and Co-Founder, OneD Battery Sciences.
This article originally appeared on Forbes.com
EV sales are growing at an accelerating pace but still represent a small number of new car sales in most markets. This is not surprising; most people cannot afford them. In the U.S., 80% of new cars are sold at an MSRP below $40,000. In 2022, Porsche Taycan sold less than 6,000 units in the U.S. and Tesla sold 20 times more Models 3 and Y than Models S and X.
What is missing are EV models with an MSRP of less than $30,000, a range of at least 300 miles and a charging speed of less than 10 minutes to get from 20% to 80% of full charge (approximately 180 miles of range).
Let’s first do some quick math to identify the challenges original equipment manufacturers (OEMs) face today in building this affordable EV. In general, today’s most efficient EVs require at least a 75 kilowatt-hour (kWh) battery. Based on my industry knowledge, the battery manufacturing costs are about $10,000 for a battery this size, more than one-third of the manufacturing cost of the entire EV. The size of the battery must be reduced to fit in smaller cars, but the battery’s energy storage capacity must be maintained and its cost must be reduced.
The EV battery charging speed is limited by several factors, including the charging power of the charging stations and the maximum safe charging rate, beyond which the cells in the battery pack are damaged. Even using 50-kilowatt DC fast charging, charging a 75-kWh battery from 20% to 80% would take almost one hour. Faster charging rates are limited by the graphite in the anodes of the EV cells.
Many people interested in buying affordable EVs do not have a garage equipped for fast charging during the night. If “affordable EVs” are sold by the millions, the charging network will quickly become the bottleneck, unless charging speed can safely be increased.
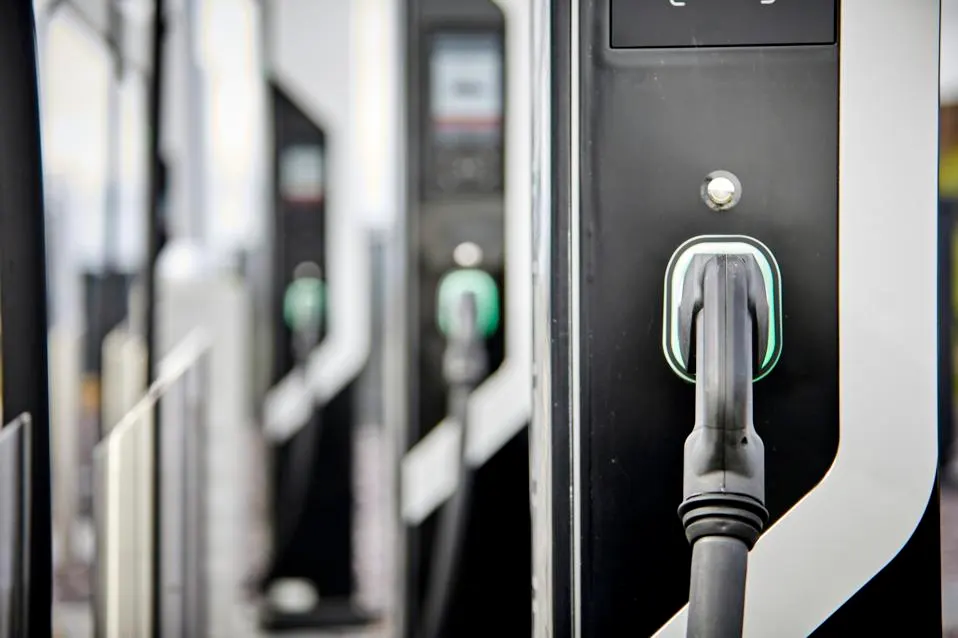
Approaching Silicon as a Solution
One option that stands to address these concerns is silicon. As a brief background, there is an abundance of silicon as a raw material, and it is the second most abundant element in the Earth’s crust, keeping supply inexpensive and essentially unlimited. Manufacturing processes have also been perfected to remove impurities. For example, silane gas (less than 99.9999% pure silane) is used to convert metallurgical grade silicon (98% pure) into polysilicon for semiconductors and solar cells, with annual global production now reaching one million tons.
These factors have been the economic fuel that created the benefits we all enjoy in our daily lives today and the disruptive force that transformed the computing, communication and energy sectors. By carefully leveraging the technical and economic aspects of silicon technologies, the impact on EV batteries can also be profound. This requires leveraging suppliers in the EV supply chain with precursors, processes and equipment from the solar supply chain.
How can silicon be the answer to these constraints?
Silicon has transformed computations, communications and renewable energy generation. In these applications, silicon enables dramatic increases in performance, with huge production volume increases driving huge cost reductions.
The impact has been described as “exponential economics”—powerful network effects driving orders of magnitude changes in performance and costs during each decade. For example, global photovoltaic installation (solar power) increased from less than 10 megawatts (1982) to more than 260 gigawatts (2022), a 20,000-times increase in four decades. During this period, cost decreased more than 100 times, from $20 per watt (1982) to less than $0.2 per watt (2022).
The Challenges with Silicon
Although silicon can store 10 times the energy of graphite alone, previous attempts to include more silicon in the anode have led to the issue of silicon expanding and breaking. The material’s tendency to expand during the charging cycle can cause the silicon particles to crack and can damage the layer of the solid electrolyte interface.
Existing methods to solve this problem have been limited due to high manufacturing costs and the lack of compatibility with the wider EV supply chain. To date, cost and technical challenges have limited the amount of silicon that can be added to EV batteries, thus leading to only modest improvements in battery performance.
The challenge is how to incorporate silicon in a way that will derive the most performance for EV batteries, and do it within the constraints of a constantly pressured cost structure.
How can these processes be applied to EV batteries?
First, existing large-scale silane production can be used to add nano-silicon inside the pores of EV-grade graphite from EV-qualified suppliers. This combines two materials already produced at scale with high purity and low cost.
Second, the combination can be accomplished with “CVD” equipment already being used in solar cell factories, to reduce the capex costs and risks. The process can use nano-catalyst to decompose silane gas into nano-silicon and hydrogen. The use of a catalyst reduces the processing time and energy required and ensures that 100% of the silane is converted into nano-silicon and hydrogen. The latter can then be reused to make more silane, reducing cost and waste.
Third, novel coatings can be applied to the silicon-graphite powders, enabling dry electrode coating, which reduces cell manufacturing costs.
With this approach and based on my company’s internal testing, the amount of graphite per EV drops by two-thirds, the anode cost drops by half, and the battery charging speed can be increased three times. While today’s EVs run on lithium-ion batteries, these prices have soared. The second half of this decade will focus on the era of making EVs affordable.
To achieve this, OEMs should consider technology solutions that cost-effectively add more silicon to the anode. This means technology that can be seamlessly integrated into existing supply chains and manufacturing processes to help significantly reduce costs.
This article originally appeared on Forbes.com